A couple of years ago Polymath Perspective ran a three-part interview with Industrial Designer Rick Dickinson, who made his name working for Sinclair Research Ltd in Cambridge, developing the ZX81, ZX Spectrum, and Sinclair QL home computers and the TV80 flat-screen pocket television. This time we are looking exclusively at Rick’s most recent design projects, finding out why they are important and what difficulties each product presented.
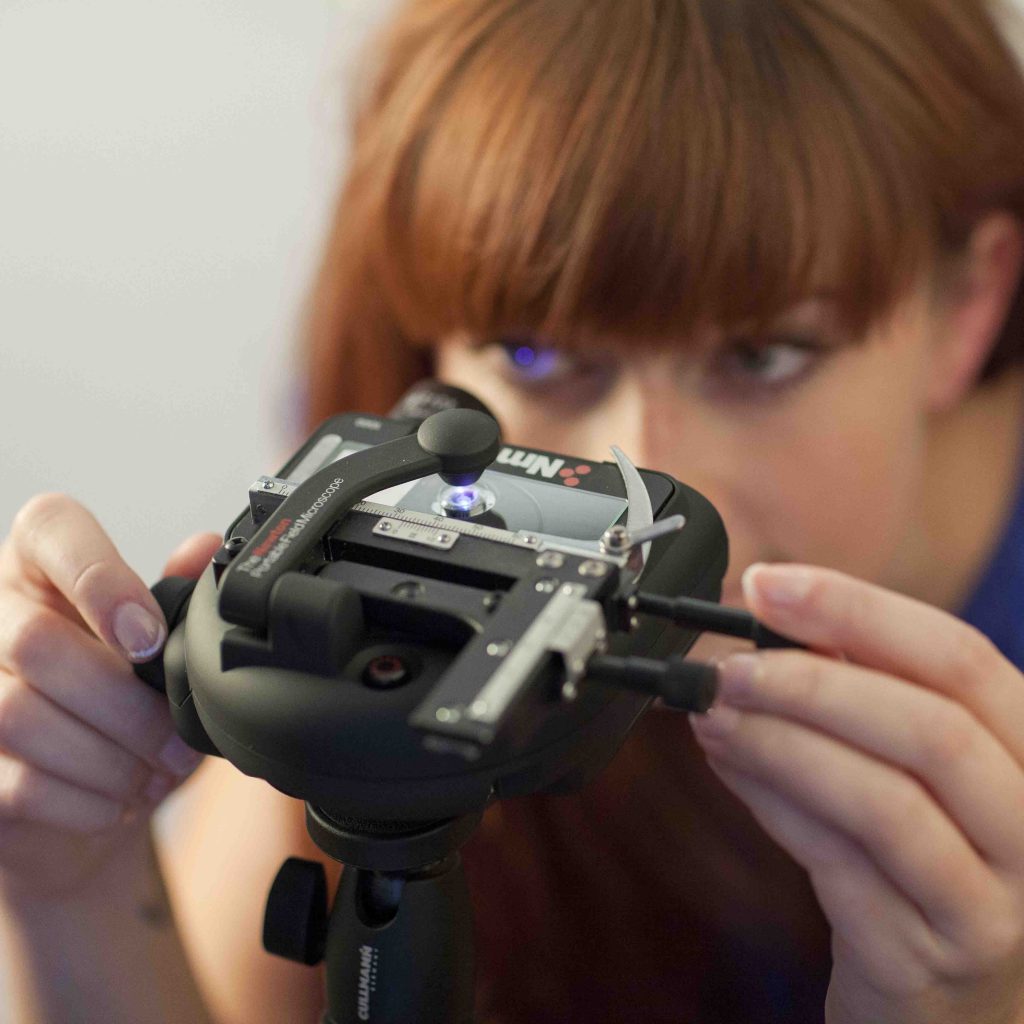
Developing Nations scope in use
The ‘Developing Nations’ Newton NM1 portable microscope for in-the-field medical diagnosis of neglected tropical diseases and malaria.
The first of Rick’s designs is something which could have a significant and positive effect on the healthcare of people living in poor countries, for it is a low-cost field microscope that is capable of up to 1000x magnification. Rick, who has been involved with the design of microscopes of different kinds for many years, explains how the project came about.
“In the late 1980s I met a man called Dr John McArthur, who is renowned for pioneering the world’s first ‘pocket’ field microscope. He designed the principle in a Japanese prisoner of war camp. He was a medical doctor, not an engineer, but he came up with this idea, made some prototypes and then produced his own microscope, unsurprisingly called The McArthur Microscope. The microscope was intended for field use in disease-ridden poor countries, where you have malaria, tuberculosis, and what we call NTDs – neglected tropical diseases. Because he and his family were medically orientated and frequently worked abroad in these sorts of areas, they could see a need for a portable field microscope to do on-the-spot diagnosis.
“You can still get them today,” continues Rick, “but they have always been staggeringly expensive to buy. Even when the microscope first came out it was about £1000 and would be three or four times that price in today’s money. McArthur designed the product well enough – it functioned and you could see malaria through it – but he couldn’t get the price down, so it was utterly unaffordable. It needed to be many orders of magnitude cheaper.”
Cutting Costs
Eventually McArthur hatched a plan to develop a low-cost version of his field microscope, and set to work finding ways to simplify the design whilst still retaining its functionality. It was when he started looking at ways to turn the idea into something that could be mass produced at a low cost, that he sought help from Rick.
“He had done a redesign and come up with a very much reduced, cut-down version, done in quite nasty plastic mouldings, which got the price down,” explains Rick. “It was not a nice instrument but it was cheap and worked. In fact the BBC Open University took a version of it for one of their programmes on microscopy. I was brought in to prepare that design for mass production, but sadly John died before we were able to do that.
“But a couple of colleagues and I were inspired to go on and produce a small microscope which we called the Lensman. We re-engineered it with our own money. It came out in the early 1990s, won some design awards and was on TV a lot, so that was around for a while.
“The problem was that it was not a very powerful product. It would magnify up to 160 times, which has its uses, but not so many on the medical front. We just couldn’t find a way of getting higher magnifications for a low enough price on such a small scale.
“To cut a long story short, a chap who was using the Lensman microscope for looking at schistosomiasis approached us one day and said that if we could make it do 400 times it would be a fantastic product. We told him it was possible but we’d need to totally engineer it and we didn’t have the funds to do that and go to manufacture. Nevertheless, we then made a series of self-funded prototypes through different organisations and gradually got bigger and bigger grants.”
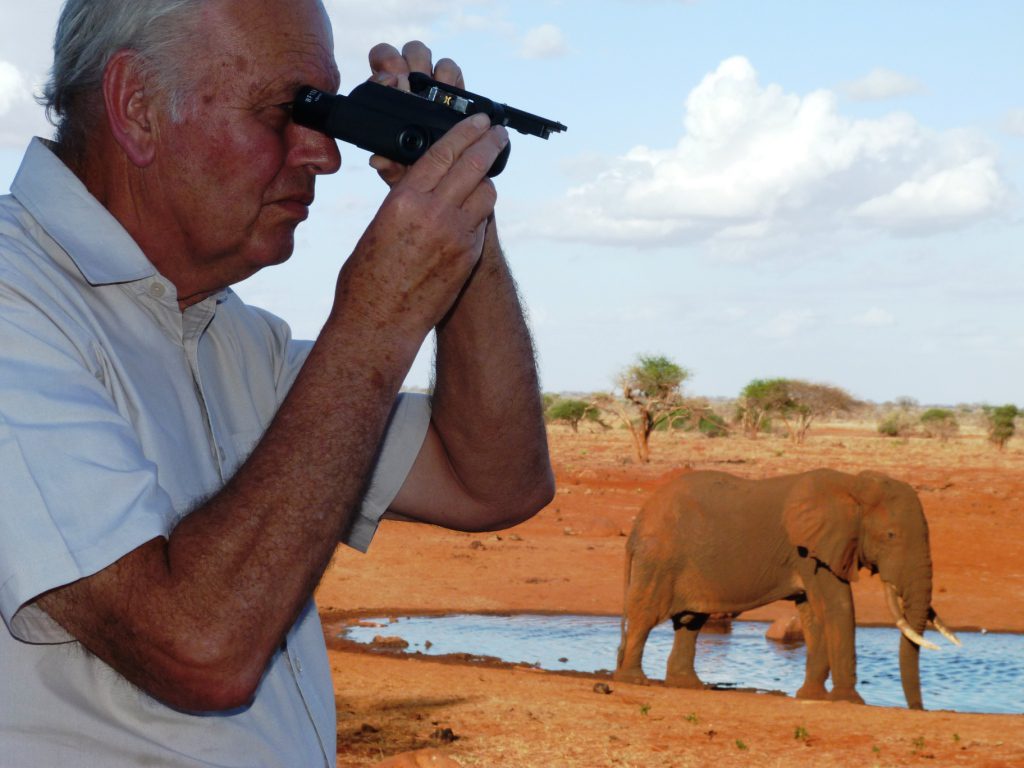
The Newton on trial in Africa
The Essential Requirements for Field Diagnosis
Rick and his colleagues came to the conclusion that in order for their microscope to be a viable and useful product it needed to satisfy three main essential requirements. The first thing it needed to be was affordable, although quite what constitutes affordable is always going to be a matter for debate.
It also needed to meet certain performance criteria. To satisfy the aforementioned scientist studying schistosomiasis it had to be able to magnify 400 times, but that still didn’t show the potentially deadly malaria parasite, which only becomes identifiable at roughly 1000x magnification. Ultimately, the team decided to increase the optical specification so that the scope would be useful in malaria diagnosis.
“1000 is pretty much the highest you can go with an optical microscope,” say Rick. “That’s because you are getting to the limits of the wavelength of visible light. If you go beyond 1000 you are starting to split the light up and you’re not really going to see much, which is why electron-beam microscopes were invented.”
The third essential requirement stated that the microscope had to be as small and light as possible in order for it to be genuinely portable.
Each requirement on its own would have been easy enough to satisfy, but meeting all three proved to be quite a challenge, and so the product took a long time to develop.
Now on sale at the Newton Microscopes website, the microscope goes for anything from just over £400 to a little over £600, which certainly seems to qualify as affordable. The reason for the variation in price is simply that the customer has a choice of which objective lenses and accessories they would like fitted to their microscope, as Rick explains.
“It depends on how you configure it and which lenses you have fitted. What I discovered is that microscopy is incredibly application specific. So, for example, if you are a malaria researcher, you need 1000x magnification and are likely to use a thing called oil immersion, which is where you close the gap between the end of the objective lens and the blood smear specimen with a blob of oil to get the air out and change the refractive index. So if you are doing malaria you are at the limit of everything and need that.
If you are looking at schistosomiasis, on the other hand, you wouldn’t be interested in 1000x magnification; you’d probably be happy with 400. Or, if you are looking at eggs or larvae you might be happy with just 100. Depending on what you want to look at, you could be carrying and paying for needless specification, so we have configured it so that you can buy it with different lenses. We currently offer four types of lenses, giving you magnifications of 100, 400, 600 and 1000x. What you can also do is change the eyepiece – that is just a standard push-in item that you can buy on any optical website – so you could, for example, have just a couple of objective lenses, but change their magnification using two different eyepieces.”
Although there are four objective lens options available, the design accommodates just three at a time and they have to be pre-fitted before shipping. Rick explains why the design does not allow users to swap and install their own lenses, and has just three slots for them instead of four.
“We tried to make it so that users could swap them but it required a lot of space for a hand to gain access to each objective lens and we already had to miniaturise the objective lenses to get the size of the product down. They can be changed, but it is not a user-friendly thing, so you have to buy it pre-configured, unfortunately. Four or five lenses would be more typical of a lab instrument, but with four or five we would not have had a small enough product. It was no larger to have three than two, but to go from three to four, the effect it had on the scale of the product was almost exponential.”
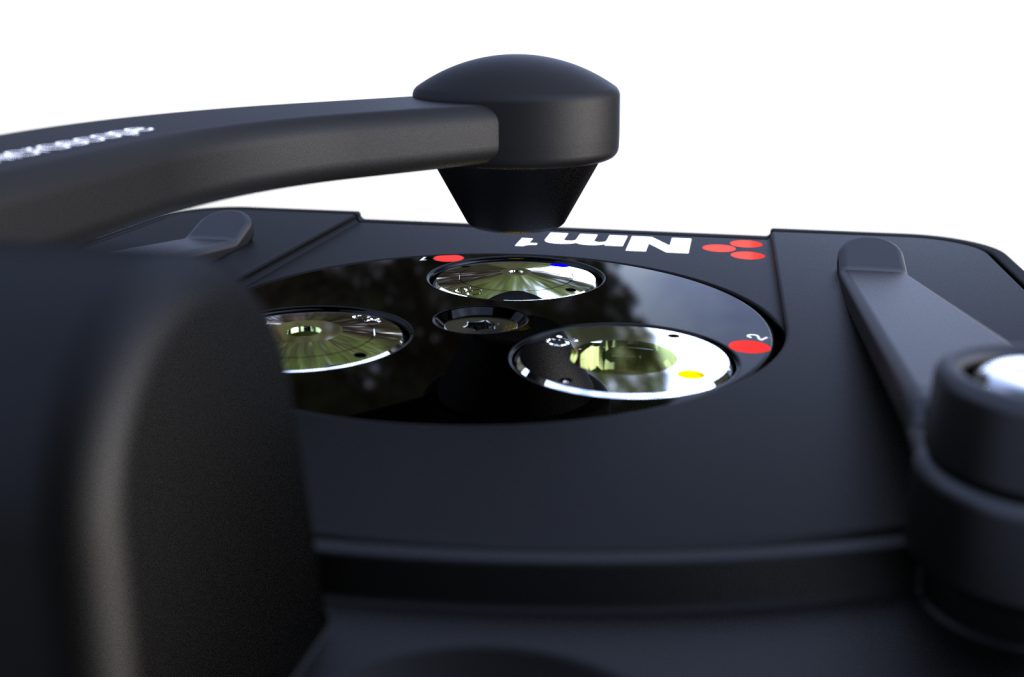
This close up shows the lighting arm sitting above one of the three objective lenses
Development and Production
Rick and his colleagues knew that in order for the Newton NM1 to be a success it needed to meet their affordability, performance and scale targets, but they were also under pressure from the Wellcome Trust, which would not grant funding until a series of trials had been competed. “To do the trials properly,” says Rick, “we had to make a range of prototypes, and in order to get the consistency between them we had to tool up quite a range of parts.
“It is always costly to tool up parts but for some things it is the only way you are ever going to get the features, functionality and, more importantly, the repeatability.
“So we did some trials at the Liverpool School of Tropical Medicine, looking at malaria. The trials were equivalent trials to see how it compared to £6000 Zeiss microscope, and we found that you could see just as much.”
The most important element in any optical system, be it a camera, telescope or microscope, is the lens assembly. As far as microscopes are concerned, this typically comprises an eyepiece, made up of an eye lens and field lens, a body tube leading to the objective lens, which is actually a container made up of a great number of individual lenses, and then a condenser lens, which, again, is composed of two or three lenses.
Before Rick and the team could really get to grips with the rest of the design it was essential that they found a manufacturer that would supply the accurate and high-quality lenses they needed to achieve 100 to 1000x magnification. The problem being that the lenses had to be unusually small for the product design to remain portable.
Rick: “If you take, say, three standard objective lenses that you find on any microscope anywhere in the world – they are all the same in principle because it is a global standard – and arrange them together to form a triangle, they take up a massive area, and by the time you put in some sort of mechanism that rotates them so you can dial in whichever one you want, and a focussing mechanism and lighting system, you have a product that’s about as big as a bench microscope! So we had to miniaturise them and the difficulty was finding a manufacturer to do that.
“A lot of people don’t understand what you are doing and are not interested. The volumes that we wanted were very small, relatively speaking, so people were simply not interested in the business. But eventually we found a company in China that already makes lenses, and we’ve since discovered that it is one of China’s largest optical manufacturers. They made us some prototype objective lenses and we went through various versions of those until we got what we wanted. The quality is just the same as a larger lens.
“Without the lenses you just don’t stand a hope really. They’ve got to be spot on: the quality of the glass, the coatings and the alignment. So the glass is all laser aligned and then set within a lens mount.
“We supplied the manufacturer with a specification for the working distance of the lens, which included, for example, the mechanical parameters and the sort of resolution we were looking for. It was then their problem to figure out how that was going to happen, so we didn’t get involved in that side of things. The manufacturer fits the glass into custom-designed lens holders and supplies us with very small objective lens assemblies that we simply screw in place, like you do on a normal microscope.”
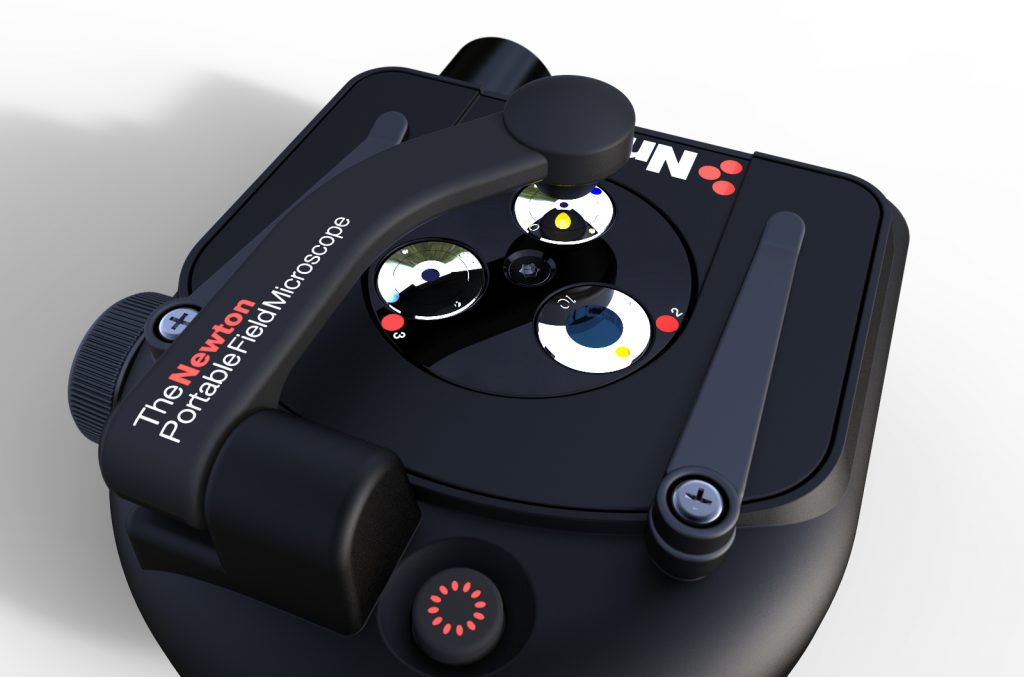
Viewed from above, the three objective lenses can clearly be seen
Form Follows Function
The appearance of the Newton NM1 is very different to that of a traditional microscope, looking more like a miniature record player than a piece of scientific equipment. Its unconventional appearance is aesthetically pleasing, but the reason it looks that way is more to do with it having to be compact and portable than looking good.
“It is what you call an inverted microscope,” Rick explains. “With normal microscopes the lens is face down and the optical tube is just a straight path above. So you’ve got the lens at the bottom looking down on the specimen, and 160mm above that you have the eyepiece. That has been standard, really, since Leeuwenhoek designed his microscope. The standard design also has a table, or stage, beneath the optical tube, but because ours is an upside-down microscope and all the optics are underneath, our stage is totally uncluttered and has very little above it.”
The one part that does sit above the specimen table, looking a bit like the stylus arm of a record player, houses a bright light, powered by three AAA batteries. “At higher magnifications you need to pump in a lot of energy so that you can see the specimen,” continues Rick. “So you lift up that lighting arm, put your sample slide on the stage, just over the objective lens, and squirt light down through the slide and whatever is on it. That passes into the objective lens and that gets bounced around a few mirrors inside. The mirrors fold up the optical system, to keep it compact.”
Once inside the Newton NM1, the optical path deviates away from the object lens at a right angle, and then makes its way towards the eyepiece via a series of mirrors which bounce the light in a zigzag shape.
“It’s a three dimensional zigzag as well,” insists Rick. “We’ve got an application for a patent on that. The crucial bit is the third dimension. As soon as you drop under the objective lens you have to divert to the side otherwise you’d have a deep product. Then we fold it up a few times.”
Another innovative aspect of the design is the system used for controlling the microscope’s focus. Traditional microscopes use a rack and pinion focus mechanism, some even offering dual controls, where the first establishes a rough focus and the second enables fine adjustment. Rick’s team concluded that such mechanisms would be too expensive to manufacture and would detrimentally increase both the size and weight of the product. They decided to look for a different method of controlling focus and came up with something rather interesting.
“We ditched the rack and pinion type method because with it we would not have a portable or low cost product,” explains Rick. “We came up with a single focus control that rotates a cam, raising the objective lens carrier up and down to focus the lenses. It’s a continuous focus design, which means that you can’t go in the wrong direction because one full turn of the focus wheel in either direction delivers the full focus range, and there are no end stops. The old rack and pinion system has no way of telling you in which direction to turn the knob to find focus, so it’s a 50/50 chance that you’ll go the right way, and if you turn the wrong way you only find out when it reaches the end of the rack and you have to come all the way back past where you started. That is very tedious.
“Our design deals with the coarse and fine variations by the accelerating and decelerating effect of the cam profile, depending on where you are on the cam. This idea was a real breakthrough in miniaturisation, weight and cost for us and we are fighting to get a patent on it.”
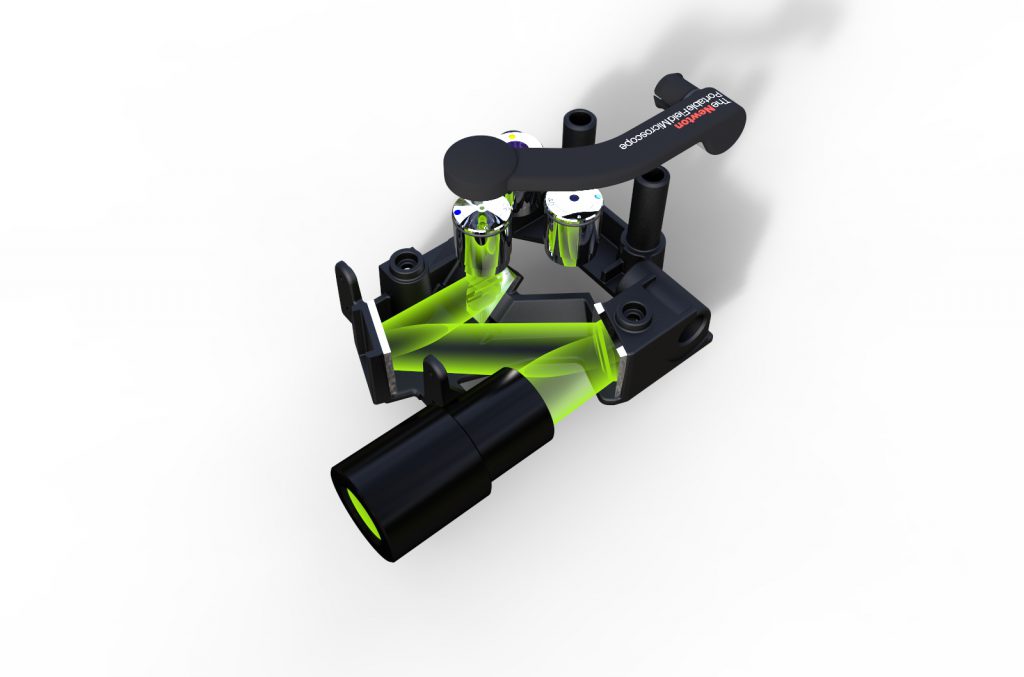
This picture shows the zigzag light path within the microscope, from the eyepiece at the front to the objective lens behind
Taking the Knocks
One of the essential characteristics of a product that is for use in the field is that it is capable of withstanding a few knocks while it is transported around from place to place. Obviously, one way to make a product robust is to encase it in something extremely tough, like metal, but Rick was also very aware that the microscope couldn’t be too heavy or large. His solution was to try to reduce the mass of the object so that if it was dropped it would hit the ground with less force.
“A beetle is light, so it can fall a distance that is many times it own body length and still be fine when it hits the ground,” explains Rick, “but a human being can’t even fall over without hurting itself. That’s the principle I applied to the design, so it was all about using lightweight materials wherever possible, although I couldn’t go as far as I wanted because of certain limitations. For example, although we’d miniaturised the objective lenses, the manufacturers still had to make them in the traditional material that every objective lens holder is made in, which is brass. That’s because all their production processes are set up for brass. We would have liked to use aluminium or magnesium but unless you can give someone an order to go and make a million of them, no one is interested in investing in changing their methods of manufacture. These are the kinds of problems you have if you are doing something new!
“So we are stuck with brass lenses which are very heavy. The rest of the product is different. Internally the chassis parts are high-pressure die-cast aluminium. Pressure die-casting gives lots of features and good repeatability. Aluminium is better than, say, zinc, in terms of weight, but zinc would actually give better definition. It is just too heavy. Ideally we would have liked magnesium but, again, it is an industry that is not particularly well serviced. There are magnesium die-casting foundries around, but few compared to zinc or aluminium, and it’s very specialised. We just couldn’t find a manufacturer that was interested in our small quantities.
“So the three shiny circular plates that you see on top of the Newton are chrome-plated brass lens holders. There is a lot of brass in there and obviously the glass is heavy too. Plastic lenses wouldn’t have been possible: you can’t get the quality with plastic and also you’d have to do the tooling for an injection mould, which would be hideous.”
Despite the problems with heavy brass objective lens holders, the Newton NM1’s outer plastic casing is one aspect of its design which is truly lightweight.
“If you strip the casing off you find a totally self-supporting microscope structure inside,” says Rick. “The plastic is there for two main reasons. One is to protect everything that is inside the microscope, and the other is to keep out the light. The plastic casing is attached to the chassis in a way that it gives quite a lot of resistance to shock. The idea is that it won’t transmit those forces into the optical or mechanical systems. So the plastic is intended to absorb the energy by bending. It’s just the same plastic as a mobile phone: what we call PC/ABS, so it’s a blend of Polycarbonate and Acrylonitrile Butadiene Styrene.”
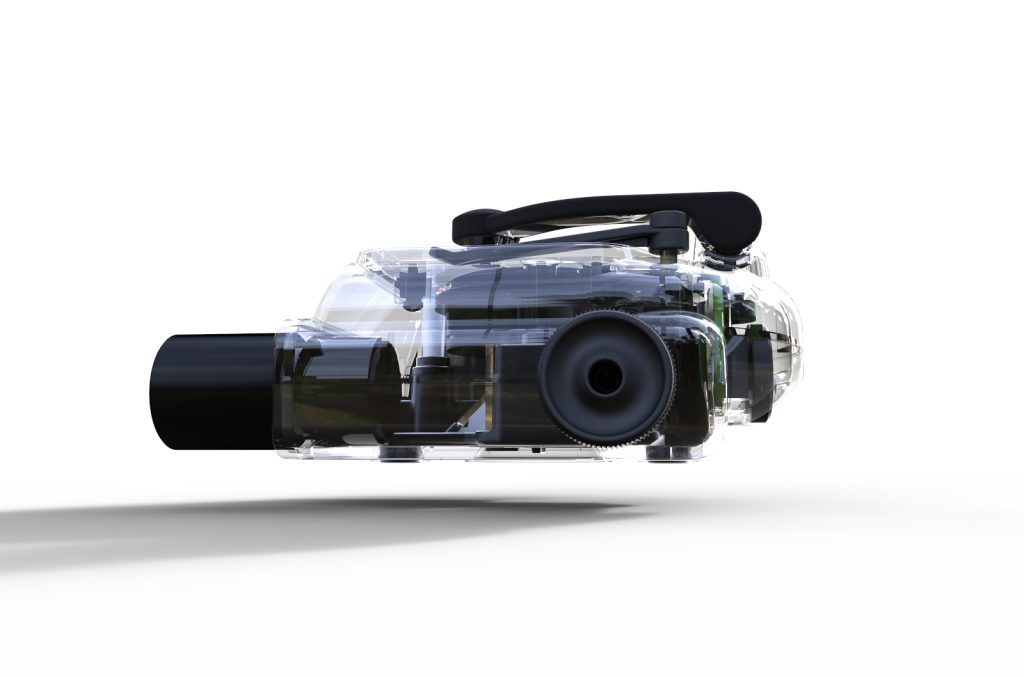
Rick: “The clear case is just a publicity shot to show the insides, it could never work like that, except in the dark.”
Taking it to Market
Unlike some of Rick’s work, the Newton NM1 is a project he and his colleagues have been involved with from start to finish. The final stage is distributing and selling the product, whether that’s direct to individuals, or as package deals with pharmaceutical manufactures, educational establishments and medical missions.
“We are doing the whole thing,” insists Rick. “We had the idea, got funding, made the prototypes, trialled them in a laboratory, in the field in Africa and various places; we’ve gone to manufacture, and now we are just in the process of launching it and looking for distributors. The website has gone live and there is an on-line shop.
“Obviously you have got to claw back your investment, but some of the proceeds allow us to give what we hope are going to be very large discounts to the people who we designed it for in the first place; so they are doctors working in poor countries in the field, trying to diagnose tropical diseases.
“Some of those organisations can’t afford to spend £6000 on a microscope and when they do, it is kept in a room. And something as simple as a lighting failure could render it useless. But if we can give them microscopes at heavily-discounted prices, say a couple of hundred pounds – that sort of thing – it could seriously change things.” TF
Rick Dickinson: Designer Update (Part 2) can be found here: Part 2